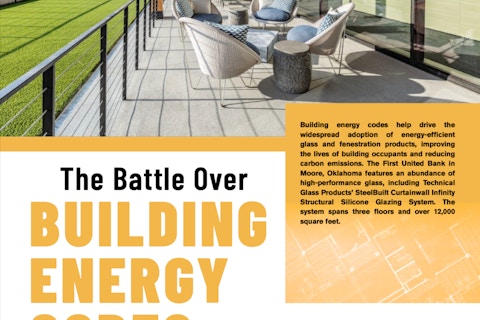
Modern product design philosophy drives any creator toward a longer view. The old basics of identifying a market opportunity remain critical, but developing a team that can properly define the problem, develop a solution, and a plan to validate results is still an emerging skill.
In the construction industry, the market opportunity is clear: consensus on climate change, volatile energy markets are driving demand for sustainable, resilient, and digitally coordinated buildings.
From Owner, to Architect, to Builder, to Operator, we face an opportunity to conceptualize, plan and deliver a new level of product where static and dynamic elements operate intelligently to preserve earth, occupant, and dollar alike.
...owners, occupants, citizens, constructors, and governments will continue to demand more efficiency, and more proof that it is being achieved.
It is not any individual building system that will achieve this, but rather their coordinated function as one system serving the structure and form that contains them. If we hope to provide the world with sustainable, resilient, and smart buildings then façade, electrical, mechanical, communications, and life safety systems must be conceptualized together from the start of a project as the structure and architecture grows around it.
Creating organic communication between contractors, engineers, clients, and architects is a difficult task on its own, but there is the added complexity of quality assurance to address. Each component of a building’s performance design requires a plan for verification – confirmation that we have achieved a more sustainable, resilient, intelligent ‘thing’. Measurement and verification methods are the means to validate the project, and they simultaneously drive a new level of planning and digital proficiency for construction Quality Control and Assurance – by another name, this is performance accountability.
The technique of achieving the High Performing Building is very much in development, but only through a disciplined integration of energy modeling, scheduling, and lifecycle perspectives into the earliest stages of planning can we adapt building science, trade craft, and project management to a new kind of building product equipped for modern demands.
“Developing a Solution” - A Building Industry Response
‘Developing a solution’ for construction of modern buildings (particularly those with complex façade concepts) is no easy task. Beyond merely integrating the technologies, one must integrate the corporate entities, design cultures, trade skills, and operator/client understanding.
Experience continues to suggest that this needs to commence in the earliest design stages where the client’s vision for their built asset is expanded to specific solutions. While architects and structural engineers are ‘massing and stacking’, building systems engineers must move in parallel – stitching a mechanical, electrical, life safety, security, and facade plan together as the facility takes shape around it.
The image below shows a typical collection of innovative ideas facing integrated teams at the outset of a major development. Many of these ideas generate architectural/structural design feedback and for General Contractors, each requires specific planning through the iron triangle of Scope (Procurement), Time (Schedule), and Cost (Budget). Every collection of innovations will require a different collection of planning responses to resolve. Without a broad discussion early in the project, much of this planning is forced to take place on the jobsite with little time for review, and no time for design alteration.
Of course, if the problems cannot be fixed on the jobsite, or problems simply go unidentified, then the worst-case scenario is engaged, where contractors and clients continue to struggle with a building well into its lifecycle. Better then to move all concerns to the planning table where their effects on traditional process, and on each other can be revealed.
Figure 1 - PCL Diagram - Response to Innovation
By driving early consideration of schedule, budget, and scope, a general contractor can hope to clearly communicate the details of modern high-performance building design to the individuals who will piece it together.
Figure 2 - Examples of Required Actions for Facade Innovation
Taking a simple example may help illustrate the basic flow. Passive House requires that the building envelope prove a set performance through a whole building envelope test. The mere existence of a measured target initiates a response – we cannot fail that final test, so we set to work. We need to start early enough to complete the following:
Identify key envelope/façade types and elements for testing.
Determine suitable testing and review processes to evaluate performance early in the process.
Schedule the tests / identify time relationships to identify any changes to critical path.
Adjust sequencing to ensure required mechanical equipment is powered and ready.
Procure materials, schedule personnel and labour.
Price materials for establishing temporary boundaries.
Communicate testing strategy to all affected trades.
Here, naming an envelope performance requirement set in motion a plan involving design and construction for architecture, HVAC, power, façade, and general contractor. Time really is of the essence.
Emerging from the design phase with this certainty, the well-stitched plans for metering and verification fall into place with ease.
The solution under development for high performing building facades then, involves reaffirming proper construction management principles, communicating a detailed plan, and building our competence with digital tools that allow constructors and operators to monitor an immense volume of quality points.
CONCLUSION
As the technology for simulation expands, so must our ability to measure the reality. With the IEA (International Energy Agency) reporting a year-on-year uptick of building energy consumption, owners, occupants, citizens, constructors, and governments will continue to demand more efficiency, and more proof that it is being achieved. Experience with current innovations has demonstrated a need for a robust, detailed, multidisciplinary discussion early – a deeper commitment to integrated process.
Modern high performing buildings require a significant investment in planning and communication. The exciting innovations in energy and façade systems are truly disruptive to the construction process. They cannot be neglected or addressed late.
Looking backward, these emerging “disruptive solutions” must be subjected to planning fundamentals under time, scope and budget. Looking forward, they must be subjected to consideration of the unknown, planning for non-fundamentals – areas where new collaboration between disciplines and individuals is required to assure a newly introduced measure of quality.
Search our extensive library.
All emails include an unsubscribe link. You may opt out at any time. See our privacy policy.