The Carapace Pavilion
A Parametric, Diagrid, Anticlastic, Thin-Shell, UHPC Prototype
Presented on October 13, 2022 at Facade Tectonics 2022 World Congress
Sign in and Register
Create an Account
Overview
Abstract
The Carapace Pavilion is a university-based, design-build, full-scale custom prototype for a possible replacement of the standard precast concrete toilet facilities that are found throughout the USA National Park System. The prototype was designed for Joshua Tree National Park in Southern California. The project is a parametric design (with performance-based reasoning for the parametrics - not just a cool shape) using a custom software scripting tool created by a graduate student. The geometry uses a diagrid structure and an anticlastic shape for strength. The use of ultra-high-performance concrete (UHPC) allows the thin-shell to be only 2” thick in places while containing no conventional rebar. The design and fabrication process was 99% paperless. Under the guidance of two university faculty, students designed and fabricated (until COVID) the project, including using digital fabrication driving a CNC machine operated by students to craft the mold. The project was prefabricated offsite to lessen site impacts and will involve a one-day installation. Project dimensions were constrained by the maximum size and weight restrictions governing transportation to the site from the precast plant. The project site uses a raised-bed foundation and earth-anchors to avoid disturbing the native-cultures artifacts known to occur in the general region of the site in the national park, and the concrete has been color-matched to the existing rock formations of the site. The design allows for all five UHPC panels of three different types to all be cast in a single mold using only one deck at the precast plant. The case study includes lessons learned from the parametric and digital processes and also the UHPC casting and fabrication.
Authors
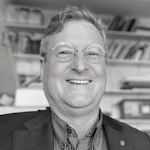
Douglas Noble, PhD, FAIA
Associate Dean
University of Southern California School of Architecture
dnoble@usc.edu
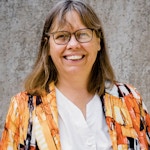
Karen M. Kensek, DPACSA
Professor of Practice in Architecture
University of Southern California School of Architecture
kensek@usc.edu
Keywords
Introduction

Seeking a substantial challenge for their students, faculty of the School of Architecture at the University of Southern California selected a real design-build project involving innovative materials and structures, a student-created custom parametric design tool, a collaborative and paperless design process, and a demanding client expecting the highest quality for installation in a national park. The small project was carried out with a combination of design studio students and a follow-up fabrication seminar. The design studio was preceded and coincided with a graduate research thesis project involving the creation of a design software scripting tool. The focus was on the design, tectonics, and fabrication of a prototype building enclosure shell.

Program and Site
Designed and built by the students and faculty, the Carapace Pavilion is an experimental prototype replacement thin-shell enclosure for the standard double-restroom buildings installed throughout state and national parks. The
Access Restricted
Design Team Structure
Design-build projects, especially those that end up spanning more than one semester, are notoriously difficult to accomplish in a university setting. The primary challenges include the tight semester schedule, external
Access Restricted
Project Scope and Educational Purposes
The project was conceived as framework for crafting multiple deliberately challenging design and fabrication processes to push the limits of materiality, computation, design, and fabrication. The task was to create
Access Restricted
The Design Process
Several constraints were established prior to the start of the studio. The program for the Carapace was determined to be a "twin" toilet vault building comparable in scale and use
Access Restricted
Custom Design Support Tool
Knowing that students would want to have substantial design freedom within the challenging constraints, a scripted software tool was developed by a graduate student that incorporated the basic design guidelines
Access Restricted
Design Iterations and 3D Printing
The design of the Carapace Pavilion was heavily influenced by the fabrication constraints and the plan to cast five panels of three types in a single mold. Multiple iterations of
Access Restricted
Design Proposal
The final project is composed of one foundation panel, two identical yet asymmetrical wall panels, and two identical roof panels. The panels assemble based on rotational symmetry (like an aircraft
Access Restricted
Foam Mold Panels Fabrication
Fabrication called for five UHPC panels to be cast using one cleverly designed mold on a single deck in the precast facility. The mold was designed and digitally fabricated by
Access Restricted
Mold Assembly
The fabrication of the mold and the casting of the panels was completed offsite at the precast plant to avoid having an on-site construction yard in the national park. To
Access Restricted
Materiality and Casting
With compressive strength exceeding 25,000PSI,*2 the ultra-high-performanceoncrete (UHPC) used*3 allowed the development of a shell that is only two inches thick at the most structurally significant section along the panel
Access Restricted
Panel Finishing
Each completed panel was extracted from the mold and set aside for additional curing. Extraction of each panel was surprisingly straightforward. Compressed air was injected between the UHPC panel and
Access Restricted
Panel Assembly
The difficulty of grinding UHPC for panel finishing, combined with the limited availability of the students and faculty to physically work on the panels, resulted in a longer than expected
Access Restricted
Transportation and Installation
The installation site for the first prototype is a somewhat hidden “VIP campground” in Joshua Tree National Park (VIP is the National Park Service acronym for “Volunteers In Parks” and
Access Restricted
Conclusion and Awards
The Carapace Pavilion represents a deliberately challenging university-based design-build project. The students, faculty, and professionals collaborated to craft a project that presented challenges in design, computation, digital fabrication, materiality, assembly
Access Restricted
Acknowledgements
Project Credits
Project: Carapace Pavilion, Joshua Tree, California
Client: National Park Service
Sponsor: The PCI Foundation, PCI West
Precast Partner: Design and fabrication primarily by students and faculty, with pro bono guidance and hands-on participation from dozens of precast experts at Clark Pacific
Engineer: Pro bono services provided by Walter P Moore engineers
Panel Connectors: A gift from JVI, Inc.
Emergency funding: More than 200 alumni and friends of the USC School of Architecture contributed when we lost one panel during casting and needed more supplies
Size: 12 ‘ wide, by 12’ high, by 42’ long (about the size of a tyrannosaurus rex)
Cost: All design and construction labor was donated. Materials and transportation costs were less than $100,000
Rights and Permissions
Boake, Terri Meyer. Diagrid Structures: Systems, Connections, Details. Walter de Gruyter GmbH, 2014
Fehling, Ekkehard, et al. Ultra‐High Performance Concrete UHPC, Wiley, 2014.
Kaiser, Harvey. The National Park Architecture Sourcebook, New York: Princeton Architectural Press, 2008.
Kanaani, Mitra. The Routledge Companion to Paradigms of Performativity in Design and Architecture: Using Time to Craft an Enduring, Resilient and Relevant Architecture, Routledge, 2020.
National Park Service. Genius Loci, The Spirit of the Place: Design Guidelines for Joshua Tree National Park, 2021 draft version, 2021.
PCI, PCI Design Handbook: Precast and Prestressed Concrete, Precast/Prestressed Concrete Institute, 2017.
PCI, PCI Architectural Precast Concrete, Third Edition, Precast/Prestressed Concrete Institute, 2007.