Printed Facades?
Cases Of Additive Manufacturing In The Building Envelope
Presented on October 13, 2022 at Facade Tectonics 2022 World Congress
Sign in and Register
Create an Account
Overview
Abstract
While additive manufacturing (AM) offers unprecedented freedom of design and a remarkable potential for material efficiency and lightweight structures, it rarely surpasses stages of art, design, or feasibility studies, and hardly ever makes its way into mass production. Compelling reason for this is that the benefits of the technology – one-off solutions, specific designs, tailored machinery – make it particularly expensive and complex. Hence, regardless of its vast number of advantages, engineers and product designers struggle to define business cases for the technology. The present work investigates the ingredients that are necessary for a successful industrial application of additive manufacturing in the building sector. Using the examples of 3D printed structural glass, reinforced thin-sheet façade panels, and nesting bricks that can be integrated directly into facades, we show that business cases for additive manufacturing in the building envelope exist. The study shows that the technology is of particular advantage when it provides functionality that is not accessible with other methods.
Authors
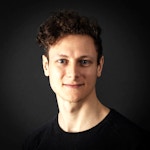
Philipp L. Rosendahl
Institute of Structural Mechanics and Design, Department of Civil and Environmental Engineering
Technical University Darmstadt
rosendahl@ismd.tu-darmstadt.de
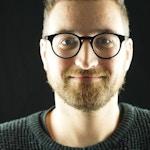
Chris Borg Costanzi
Institute of Structural Mechanics and Design, Department of Civil and Environmental Engineering
Technische Universitat Darmstadt
borg@ismd.tu-darmstadt.de
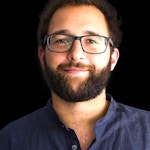
Philipp A. Chhadeh
Institute of Structural Mechanics and Design, Department of Civil and Environmental Engineering
Technische Universitat Darmstadt
chhadeh@ismd.tu-darmstadt.de
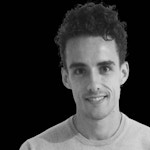
Robert Akerboom
Institute of Structural Mechanics and Design, Department of Civil and Environmental Engineering
Technical University Darmstadt
akerboom@ismd.tu-darmstadt.de
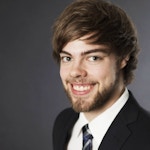
Benedikt Waldschmitt
Institute for Steel Construction and Materials Mechanics, Department of Civil and Environmental Engineering
Technical University Darmstadt
waldschmitt@ismd.tu-darmstadt.de
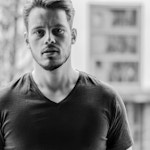
Alexander Wolf
Institute of Structural Mechanics and Design, Department of Civil and Environmental Engineering, Technical University of Darmstadt
Technical University Darmstadt
wolf@ismd.tu-darmstadt.de
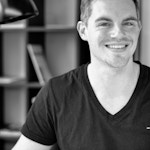
Marvin Kehl
Institute of Structural Mechanics and Design, Department of Civil and Environmental Engineering
Technical University Darmstadt
kehl@ismd.tu-darmstadt.de
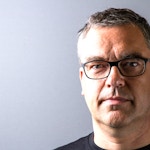
Ulrich Knaack
Institute of Structural Mechanics and Design, Department of Civil and Environmental Engineering
Technical University Darmstadt
knaack@ismd.tu-darmstadt.de
Keywords
Introduction
While additive manufacturing (AM) has matured from a technology for prototyping and the fabrication of small, individualized parts to a technology that allows for 3D printing at the scale of buildings, the largest inhibitor for its application in the built environment remains its profitability. Compelling reason for this is that the benefits of the technology – one-off solutions, specific designs, tailored machinery – make it particularly expensive and complex. Hence, regardless of its vast number of advantages, engineers and product designers struggle to define business cases for the technology. The present work investigates the ingredients that are necessary for a successful industrial application of additive manufacturing in the building sector.
Since William Urschel's patent of a Machine for Building Walls in the 1930's, additive manufacturing in the built environment has evolved as a tool for product design and prototyping and has now even reached the scale of entire buildings. Compared to traditional industrial manufacturing technologies such as milling or casting, it offers several advantages. Depending on whether and how many support structures are needed, little to no waste is generated during production (Jiang et al. 2018). Complex geometries with undercuts or cavities can be produced with virtually no increase in production cost: complexity comes for free (Fera et al., 2018). The implementation of complex motion controls has unlocked additional degrees of freedom. In this way, the print quality has improved significantly from both a mechanical and an aesthetic point of view (Jiang et al., 2021). New degrees of freedom, of course, necessitated new algorithms for path planning (Jiang and Ma, 2020). While dimensions and available materials of 3D-printed components were still limited in the early days of the technology, technical progress has unlocked large formats from a wide variety of materials (Izard et al., 2017). Recent attempts even aimed at replacing the conventional layer-by-layer with a multilayer printing process to reduce the manufacturing time (Jiang, 2020). All these developments have matured additive technologies to scales of the construction industry, which, by nature, has a need for large-format and, above all, individualized components (Kloft et al., 2021).
Applications in the built environment extend from highly specialized interconnecting nodes for free-form facades (Mohsen, 2020) to shape-optimized, large-format components made of reinforced concrete that offer the potential of more sustainable construction through the efficient and economic use of resources (Kloft et al., 2020). Additive manufacturing techniques used in the construction sector are unique with respect to both the material used and the technology applied in each case (Al Rashid et al, 2020). In addition to the typical off-site production (factory or lab), there are examples of on-site printed large structures, such as a wire-arc additively manufactured steel pedestrian bridge on the campus of the Technical University of Darmstadt (Lange et al., 2020), or an apartment building built in Beckum, Germany (PERI GmbH, 2020, 2021). In addition to terrestrial applications, additive manufacturing is considered for the construction of extra-terrestrial colonies. The space industry aims at using lunar or Martian dust and rock for the construction of permanently inhabited stations (Cesaretti et al., 2014).
These technological developments fall into a time where we witness a shortage in building materials and increasing costs for construction and the disposal of waste; a time where discussions on the environmental impact of technologies have arrived at architecture and construction. The established notion of cheap construction materials and expensive geometric complexity seems outdated. Instead, complex components that integrate several functions and transfer loads efficiently are becoming important. Yet, the largest inhibitor for the application of additive manufacturing in the built environment remains the business case. The present work explores necessary conditions for the economic use of 3D printing in the building envelope at the example of several case studies.
Methodology
The objective of the present work is the examination of three cases of possible applications of additive manufacturing in the building envelope. To assess their potentials quantitively, we formulate a
Access Restricted
3D Printed Structural Glass
Glass provides the ability to facades to establish a visual relationship between the in- and outside of a building. Whether transparent or translucent, the transmission of light through glass ensures
Access Restricted
Free-Form Façade Panels
Since the early 20th century, free-form façade panels have characterized iconic facades such as those of the Chrysler Building (New York, 1928), the Walt Disney Opera House (Los Angeles, 2003)
Access Restricted
Nesting Bricks
Owing to their many useful properties (non-combustible, readily recyclable, moisture-regulating, among others), the use of ceramic building materials goes back thousands of years. In addition to classic bricks or roof
Access Restricted
Сonclusion
Additive manufacturing has matured from a method for prototyping and the fabrication of small, individualized parts to a technology that allows for 3D printing at the scale of buildings. However
Access Restricted
Rights and Permissions
Al Rashid, A., S. A. Khan, S. G. Al-Ghamdi, and M. Koç. 2020. “Additive Manufacturing: Technology, Applications, Markets, and Opportunities for the Built Environment.” Automation in Construction 118 (February): 103268.
Cesaretti, G., E. Dini, X. De Kestelier, V. Colla, and L. Pambaguian. 2014. “Building Components for an Outpost on the Lunar Soil by Means of a Novel 3D Printing Technology.” Acta Astronautica 93: 430–50.
Chan, S. S. L., Pennings, R. M., Edwards, L., & Franks, G. V. (2020). 3D printing of clay for decorative architectural applications: Effect of solids volume fraction on rheology and printability. Additive Manufacturing, 35(4), 101335.
Chen, Z., Li, Z., Li, J., Liu, C., Lao, C., Fu, Y., Liu, C., Li, Y., Wang, P., & He, Y. (2019). 3D printing of ceramics: A review. Journal of the European Ceramic Society, 39(4), 661–687.
Datsiou, K. C., E. Saleh, F. Spirrett, R. Goodridge, I. Ashcroft, and D. Eustice. 2019. “Additive Manufacturing of Glass with Laser Powder Bed Fusion.” Journal of the American Ceramic Society 102 (8): 4410–14.
Destino, J. F., N. A. Dudukovic, M. A. Johnson, D. T. Nguyen, T. D. Yee, G. C. Egan, A. M. Sawvel, et al. 2018. “3D Printed Optical
Quality Silica and Silica–Titania Glasses from Sol–Gel Feedstocks.” Advanced Materials Technologies 3 (6): 1–10.
Federal Association of the German Brick and Tile Industry. (2019). Annual report.
Fera, M., R. Macchiaroli, F. Fruggiero, and A. Lambiase. 2018. “A new perspective for production process analysis using additive manufacturing—complexity vs production volume.” The International Journal of Advanced Manufacturing Technology, 95(1–4), 673–685.
Izard, J.-B., A. Dubor, P.-E. Hervé, E. Cabay, D. Culla, M. Rodriguez, and M. Barrado. 2017. “Large-Scale 3D Printing with Cable-Driven Parallel Robots.” Construction Robotics 1 (1–4): 69–76.
Jiang, J. 2020. “A Novel Fabrication Strategy for Additive Manufacturing Processes.” Journal of Cleaner Production 272: 122916.
Jiang, J., and Y. Ma. 2020. “Path Planning Strategies to Optimize Accuracy, Quality, Build Time and Material Use in Additive Manufacturing: A Review.” Micromachines 11 (7): 633.
Jiang, J., S. T. Newman, and R. Y. Zhong. 2021. “A Review of Multiple Degrees of Freedom for Additive Manufacturing Machines.” International Journal of Computer Integrated Manufacturing 34 (2): 195–211.
Jiang, J., X. Xu, and J. Stringer. 2018. “Support Structures for Additive Manufacturing: A Review.” Journal of Manufacturing and Materials Processing 2 (4): 64.
Klein, J., M. Stern, G. Franchin, M. Kayser, C. Inamura, S. Dave, J. C. Weaver, et al. 2015. “Additive Manufacturing of Optically Transparent Glass.” 3D Printing and Additive Manufacturing 2 (3): 92–105.
Kloft, H., C. Gehlen, K. Dörfler, N. Hack, K. Henke, D. Lowke, J. Mainka, and A. Raatz. 2021. “TRR 277: Additive Fertigung Im Bauwesen.” Bautechnik 98 (3): 222–31.
Kloft, H., M. Empelmann, N. Hack, E. Herrmann, and D. Lowke. 2020. “Reinforcement Strategies for 3D‐concrete‐printing.” Civil Engineering Design 2 (4): 131–39.
Kotz, F., K. Arnold, W. Bauer, D. Schild, N. Keller, K. Sachsenheimer, T. M. Nargang, C. Richter, D. Helmer, and B. E. Rapp. 2017. “Three-Dimensional Printing of Transparent Fused Silica Glass.” Nature 544 (7650): 337–39.
Lange, J., U. Knaack, T. Feucht, M. Erven, C. Borg Costanzi, and B. Waldschmitt. 2020. “3-D Gedruckte Fußgängerbrücke Aus Stahl.” In Baustatik – Baupraxis, Stuttgart.
Lee, I., A. Manthiram, and H. L. Marcus. 1995. “Selective Laser Sintering of Alumina-Zinc Borosilicate Glass Composites Using Monoclinic HBO₂ as a Binder.” In 1995 International Solid Freeform Fabrication Symposium, 46–54. Austin, Texas.
Mohsen, A. 2020. Design to Manufacture of Complex Building Envelopes. Vol. 56. Mechanik, Werkstoffe Und Konstruktion Im Bauwesen. Wiesbaden: Springer Fachmedien Wiesbaden.
Moore, D. G., L. Barbera, K. Masania, and A.R. Studart. 2020. “Three-Dimensional Printing of Multicomponent Glasses Using Phase-Separating Resins.” Nature Materials 19 (2): 212–17.
Nicholas, P., Zwierezycki, M., Nørgaard, E. C., Stasiuk, D., Thomsen, M., & Hutchinson, C. (2017). Adaptive Robotic Fabrication for Conditions of Material Inconsistency: Increasing the Geometric Accuracy of Incrementally Formed Metal Panels. In A. Menges, R. G. B. Shiel, & M. Skavara (Eds.), Fabricate 2017 (pp. 114–121). UCL Press.
PERI GmbH. 2020. “PERI Builds the First 3D-Printed Residential Building in Germany.” Press Release. 2020. https://www.peri.com/en/media/... (accessed October 29, 2021).
PERI GmbH. 2021. “Germany’s First Printed House Officially Opened.” Press Release. 2021. https://www.peri.com/en/media/... (accessed October 29, 2021).
Piermarini, E., Nuttall, H., May, R., Janssens, V. M., Manglesdorf, W., & Kelly, T. (2018). Morpheus Hotel, Macau - a paradigm shift in computational engineering. Steel Construction, 11(3), 218–231.
Seel, M., R. Akerboom, U. Knaack, M. Oechsner, P. Hof, and J. Schneider. 2018a. “Additive Manufacturing of Glass Components - Exploring the Potential of Glass Connections by Fused Deposition Modeling.” In Challenging Glass 6 – Conference on Architectural and Structural Applications of Glass, 381–88.
Seel, M., R. Akerboom, U. Knaack, M. Oechsner, P. Hof, and J. Schneider. 2018b. “Fused Glass Deposition Modelling for Applications in the Built Environment.” Materialwissenschaft Und Werkstofftechnik 49 (7): 870–80.
Wilfinger, M., Knaack, U., Strauß, H., & Fehlhaber, T. (2021). Ziegel aus dem 3D-Drucker. In Mauerwerk Kalender 2021 (pp. 221–239). Wiley.
Wolf, A., Rosendahl, P. L., & Knaack, U. (2022). Additive manufacturing of clay and ceramic building components. Automation in Construction, 133(September 2021), 103956.