More Than a Facade
A need for a design and testing standard for partially composite precast concrete insulated wall panels
Presented on October 12, 2022 at Facade Tectonics 2022 World Congress
Sign in and Register
Create an Account
Overview
Abstract
In 2014, the American National Standards Institute (ANSI) approved the Precast/Prestressed Concrete Institute (PCI) as an accredited ANSI Standards Developer. Since then, PCI has partnered with the American Concrete Institute (ACI) to develop and maintain a standard specification for the design, fabrication, and handling of precast and precast/prestressed concrete insulated wall panels. This panel type has been supplanting traditional hard-wall construction for many building types.
A variety of proprietary partially composite wall systems have been developed by industry. These systems use thermally efficient wythe connectors to produce lighter, thinner walls with higher R values and minimal thermal bridging between wythes. The ACI 318 Building Code does not yet specifically cover structural analysis and design procedures for these partially composite concrete members (ACI Committee 318).
To remedy this situation, PCI has funded research to determine the strength characteristics of the various commercially available wythe connector systems. Double-shear push-off tests have been and are being conducted to determine ultimate shear strength, deformation and ductility for each manufacturer's connector type. The resultant values will then be used as input for multiple proposed design and analysis procedures for this product category. If approved, these procedures will be recognized by ANSI and be included in the upcoming PCI/ACI Precast Insulated Wall Panel Design Standard.
Authors
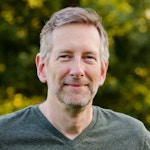
Edward Losch
PhD, PE, SE, RA
Losch Engineering
edlosch@gmail.com
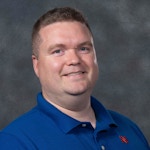
Marc Maguire
PhD, Assistant Professor
University of Nebraska-Lincoln
marc.maguire@unl.edu
Keywords
Introduction
Precast concrete insulated sandwich wall panels have gained in popularity over the years. Typical applications include schools, gymnasiums, food processing plants, justice facilities and commercial/warehouse buildings. They provide a hard, durable surface both inside and out that is installed quickly in a single operation. Panels can be designed for blast-resistance, and are often load-bearing, carrying roof and floor loads, as well as providing the lateral shear resistance for the building.
Reasons for their increased use in place of more traditional materials include:
Speed of erection: A typical warehouse can be erected in a week. Cold weather is not an issue, since the panels are cast in a temperature-controlled environment and shipped to the site when needed. Weight is reduced and smaller cranes are often allowed when compared to tilt-up construction.
Design flexibility: The casting procedure allows for a large variety of finishes and patterns, including inset brick and stone.
Thermal efficiency: Edge-to-edge, top-to-bottom rigid insulation can be used within a relatively thin wall, providing a high effective R value. The thermal mass of the concrete provides an added benefit by slowing heat transmission through the wall, flattening out temperature swings.
A typical panel has two outer concrete layers, or “wythes”, separated by rigid insulation (Figure 1), and is cast in a long-line form in a plant (Figure 2). One or both wythes are usually prestressed to reduce cracking and improve performance (Figure 3). The panels are trucked to the job site and erected with a crane (Figure 4). Panels can carry roof and floor loads or just act as cladding (load-bearing vs. non-loadbearing, Figure 5).




There are different types of panel designs to consider:
Non-composite: In non-composite panels, the concrete wythes act independently (Figure 6a). This design is typically used when a high insulation value is required, such as for a cooler or freezer building. The wythes are isolated by high-performance rigid insulation and are connected together solely by thermally non-conductive pin connectors (Figure 6b). The pins are made of either a fiberglass and vinyl ester or polypropylene plastic or other non-conductive material. The interior structural wythe is usually much thicker than the exterior face wythe.




Fully-composite: In fully-composite panels, the wythes act together as a unit for full horizontal shear transfer. A typical composite panel is eight times stiffer, can take three times the stress without cracking and has twice the ultimate strength of a non-composite panel of similar thickness. Composite panels are typically less expensive to make than non-composite panels, primarily because they can carry more loads and can be made taller and thinner. The inside and outside wythes are usually stressed with prestressing strand and made of equal thickness in order to minimize internal strains. Typically, steel truss type connectors and solid concrete sections are required to produce a fully-composite panel, although, this is not always the case in the literature (Pessiki and Mlynarczyk 2003) and it has been argued that no panel is truly fully-composite for all design limit states (Taylor Sorensen, Dorafshan, and Maguire 2018).

Partially-composite: Partially composite panels (the focus of this paper) provide less than full shear transfer between wythes (Fig. 7). They behave in a manner in-between composite and non-composite. Historically, the degree of composite action is usually determined by load tests performed by an independent testing lab or in-house by the connector manufacturer. Proprietary partially-composite wall systems have become available which combine the high insulating value of non-composite panels with the strength and slenderness of composite panels. This is accomplished using non-conductive truss, grid or individual connectors between the wythes for shear transfer. Partial composite action provides sufficient strength for most applications in much the same way partially composite floor systems are usually more economical.
Partially composite walls are typically thinner and lighter than a non-composite sandwich wall panel, while still providing excellent thermal and structural efficiency with proper detailing. Historically, walls that were designed as fully composite are likely close to fully composite structurally, but require penetration of the insulation with solid concrete sections to exhibit such behavior, making them less attractive relative to increasingly stringent insulation requirements.
Analyzing the strength, ductility and flexibility of a partially-composite panel is more difficult than for a fully-composite or non-composite design. This is because the degree of composite action varies with the span, thickness and wythe connector layout, among other factors. Bunching the connectors near the ends will increase capacity, for example, though this is not advised by most connector manufacturers for analysis reasons. Paradoxically, shorter spans require more connectors per unit area to achieve the same degree of composite action. A panel may exhibit 100% composite action for ultimate strength, but only 25% composite behavior for deflection, further complicating the analysis.
Background
Traditionally, composite wall panels have been fabricated using continuous steel wire trusses for the wythe connectors (Fig. 2). Often, solid zones of concrete are also used at the top and
Access Restricted
Method
Before a standard design method can be implemented, a standard model for the wythe connector properties needs to be developed. While different connector systems may use specialized techniques that may
Access Restricted
Data
Example connector properties are presented in Figure 13. Clearly, the behaviors of different systems provide different properties. For engineering purposes in the elastic range, the engineer requires elastic stiffness, elastic
Access Restricted
Explanation
The Beam-Spring Model is intended to be a general-purpose model that can be used for any type of connector, whether truss, bar or plate. While not adopted into any design
Access Restricted
Design Curves
It is expected that wythe connector strain curves will be provided by the system manufacturers, based on the PCI standard testing method (see Figure 15). These values can be input
Access Restricted
Conclusion and Future Work
Partially composite concrete sandwich wall panels are a rapidly growing segment of the market. These panels can be used for cladding or load bearing conditions and create a highly efficient
Access Restricted
Acknowledgements
Thank you to Fray Pozo-Lora for helping with compiling details for this paper. Special thanks for Taylor Sorensen for the thermal image picture.
Rights and Permissions
ACI Committee 318. 2014. “Building Code Requirements for Structural Concrete (ACI 318M-14), an ACI Standard, and Commentary on Building Code Requirements for Structural Concrete (ACI 318RM-14), an ACI Report.” In , 519. American Concrete Institute.
Al-Rubaye, Salam, Taylor Sorensen, and Marc Maguire. 2017a. “Full Scale Testing of Concrete Sandwich Wall Panels.” In Proceedings of the PCI National Bridge Conference,. Cleveland, OH.
———. 2017b. “Investigating Composite Action at Ultimate for Commercial Sandwich Panel Composite Connectors.” Civil and Environmental Engineering Faculty Publications. Paper 3532. https://digitalcommons.usu.edu/cee_facpub/3532.
Al-Rubaye, Salam, Taylor Sorensen, Jaiden Olsen, and Marc Maguire. 2018. “Evaluating Elastic Behavior for Partially Composite Precast Concrete Sandwich Wall Panels.” PCI Journal 63 (5): 71–88.
Einea, Amin, David C Salmon, Gyula J Fogarasi, Todd D Culp, and Mäher K Tadros. 1991. “State-of the-Art of Precast Concrete Sandwich Panels.” PCI JOURNAL 36 (6): 78–98.
Einea, Amin, David C Salmon, Maher K Tadros, and Todd Culp. 1994. “A New Structurally and Thermally Efficient Precast Sandwich Panel System.” PCI Journal 39 (4).
Frankl, B, G Lucier, S Rizkalla, G Blaszak, and T Harmon. 2008. “Structural Behavior of Insulated Prestressed Concrete Sandwich Panels Reinforced with FRP Grid.” In Proceedings of the Fourth International Conference on FRP Composites in Civil Engineering (CICE2008), Zurich, Switzerland. Vol. 2224. http://www.iifc.org/proceedings/CICE_2008/papers/2.C.2.pdf.
Gombeda, Matthew J, Patrick Trasborg, Clay J Naito, and Spencer E Quiel. 2017. “Simplified Model for Partially-Composite Precast Concrete Insulated Wall Panels Subjected to Lateral Loading.” Engineering Structures 138: 367–80.
Granholm, H. 1949. Om Sammansatta Balkar Och Pelare Med Särskild Hänsyn till Spikade Träkonstruktioner: On Composite Beams and Columns with Particular Regard to Nailed Timber Structures. Chalmers Tekniska Högskola. Elanders boktryckeri aktiebolag.
Holmberg, Ake, and Erik Plem. 1965. Behaviour of Load-Bearing Sandwich-Type Structures. Byggforskningen.
ICC Evaluation Service. 2010. “AC422 Semicontinuous Fiber-Reinforced Grid Connectors Used in Combination with Rigid Insulation in Concrete Sandwich Panel Construction.” Los Angeles, CA. www.icc-es.org.
———. 2015. AC320 Fiber-Reinforced Polymer Composite or Unreinforced Polymer Connectors Anchored in Concrete. Los Angeles, CA: ICC. https://shop.iccsafe.org/es-acceptance-criteria/ac320-fiber-reinforced-polymer-composite-or-unreinforced-polymer-connectors-anchored-in-concrete-approved-oct-2015-editorially-revised-sept-2017-pdf-download.html.
Losch, Edward D, Patrick W Hynes, Ray Andrews Jr, Ryan Browning, Paul Cardone, Ravi Devalapura, Rex Donahey, Sidney Freedman, Harry A Gleich, and Gerald Goettsche. 2011. “State of the Art of Precast/Prestressed Concrete Sandwich Wall Panels.” PCI Journal 56 (2): 131–76.
Losch, Edward D. 2005. "Precast/Prestessed Concrete Sandwich Walls: Information for the Structural Engineer." Structure Magazine. April 2005: 16-20. https://www.structuremag.org/wp-content/uploads/2014/09/C-Building-Blocks-April-051.pdf.
Naito, Clay J, John M Hoemann, Jonathon S Shull, Aaron Saucier, Hani A Salim, Bryan T Bewick, and Michael I Hammons. 2011. “Precast/Prestressed Concrete Experiments Performance on Non-Load Bearing Sandwich Wall Panels.” BLACK AND VEATCH OVERLAND PARK KS.
Newmark, Nathan M. 1951. “Test and Analysis of Composite Beams with Incomplete Interaction.” Proceedings of Society for Experimental Stress Analysis 9 (1): 75–92.
Olsen, Jaiden, Salam Al-Rubaye, Taylor Sorensen, and Marc Maguire. 2017. “Developing a General Methodology for Evaluating Composite Action in Insulated Wall Panels.” Report to PCI. Chicago, IL: Precast/Prestressed Concrete Institute. https://digitalcommons.usu.edu/cee_facpub/3531.
Pessiki, Stephen, and Alexandar Mlynarczyk. 2003. “Experimental Evaluation of the Composite Behavior of Precast Concrete Sandwich Wall Panels.” PCI Journal 48 (2): 54–71.
Salam Al-Rubaye, Taylor Sorensen, and Marc Maguire. 2021. "Iterative and Simplified Sandwich Beam Theory for Partially Composite Concrete Sandwich Wall Panels." ASCE Journal of Structural Engineering, 147(10): 04021143
Sorensen, T., S. Dorafshan, and M. Maguire. 2017. “Investigating Thermal Efficiency of In Service Concrete Sandwich Wall Panels.” In ASCE Congress on Technical Advancement. Duluth, MN.
Sorensen, Taylor, Sattar Dorafshan, and Marc Maguire. 2018. “Matrix Model Accuracy of Partially Composite Concrete Sandwich Panels.” In Proceedings of the PCI National Bridge Conference. Denver, CO.
Sorensen, Taylor, Sattar Dorafshan, Marc Maguire, and Robert J Thomas. 2019. “Thermal Bridging in Concrete Sandwich Walls.” Concrete International 40 (10).
Tomlinson, Douglas, and Amir Fam. 2015. “Flexural Behavior of Precast Concrete Sandwich Wall Panels with Basalt FRP and Steel Reinforcement.” PCI Journal. https://doi.org/10.15554/pcij.11012015.51.71.