Infinite Panel System
Light Mass Envelope Solutions for Reducing GHG Emissions
Sign in and Register
Create an Account
Overview
Abstract
Today, building facades are expected to do much more than merely provide shelter, which is driving the need for higher performing envelope solutions. Building energy codes such as ASHRAE 90.1 and California’s Title 24 have progressed significantly over the past 30 years with an increased focus on reducing carbon emissions from the built environment and requiring more energy efficient envelopes. In addition, the industry is being pressured to reduce the usage of Portland Cement. Ordinary Portland Cement’s (OPC) basic formula has not significantly changed since the early 1800’s. It is one of the most widely used man made material in the world today for the built environment. Various sources state that OPC can generate more carbon dioxide than all the trucks in the world combined.
This has driven the need for higher performing envelope solutions that are requiring lower not to exceed U values in both the opaque and window assembly designs. In addition, LEED, public and private entities are requesting concrete that use less or eliminates OPC to further help reduce the carbon footprint of this enduring material. The irony of this is both ASHRAE 90.1 and CA T24 recognize the benefit of materials such as concrete that have a much higher heat capacity than other building materials such as curtain wall and metal panel. In certain climate zones this can have a significant impact on reducing HVAC loads to a Building. Mass Heavy and Light Mass materials require substantially less insulation.
The Clark Pacific Infinite Panel Series system offers a blank palette of facade options including a light mass envelope solution to address this need. One option of the system is a Composite Concrete Architectural Prefabricated Panel system CCAPP, it is designed as a complete barrier system that features a unitized frame design with standard connections, while providing a continuous layer of insulation. The prefabricated pre-insulated panels can be provided with other skin options such as GFRC, metal panels, spandrel glass and pre-glazed thermally broken windows specifically designed for the system. The single source system for the total envelope allows for better continuity of the air, water, thermal and acoustic barrier.
This paper will study the energy performance of the CCAPP system on building’s energy related carbon emissions. Utilizing energy models from real buildings, the Clark Pacific CCAPP system was compared against various traditional envelope systems (stucco walls with punched windows, window walls and curtainwalls) for a typical office building and a high-rise residential tower. Each building was analyzed in various climate zones across the western United States to better understand the regional impact in energy usage and cost.
The unitized system also provides high STC/OITC values compared to the other systems. For fire life safety protection, the system has passed the NFPA 285, ASTM E119 for up to a 2hr rated wall assembly. A UL 263 is pending at the time of this publication. Compared to traditional cast in place, tilt up or full thickness Architectural Precast Concrete. The 2.25 to 3” concrete skin on CCAPP uses up to 67% less concrete than those solutions, does not require heavy reinforcing or an additional stud wall for interior finishes. To meet or exceed the continuous insulation requirements of ASHRAE 90.1. Spray foam insulation, which has a high R value (6.8 to 7.4 per inch). The 2-pound closed cell spray foam and precast concrete are both approved materials for use in the prescriptive air barrier requirements in CA T24. With the concretes higher heat capacity typically no more than 1.5 to 2” of spray insulation is required with no additional batt insulation in the cavity for most climate zones on the West Coast. The concern with spray foams has been the usage of hydrofluorocarbons HFCs for the blowing agent. The spray foam industry was mandated to change blowing agents from HFC to Hydrofluoroolefin HFO. This is significant, the Global Warming Potential GWP of CFCs was as high as 1,430. The GWP of HFO blowing agents is one. This combination of products along with the standardization of the details and windows make it one of the most complete barrier systems available that reduces the carbon footprint.
As an example, pictured is a full thickness 25-year-old Architectural Precast Panel in the background for a State Office building in Oakland, CA. Foreground the back of a CCAPP pre- glazed and pre-insulated panel for a high-rise mixed-use residential building close by, ready for hat channel and drywall. The work moved off site also contributes to reduced carbon emissions and traffic congestion compared to traditional on site multi trade construction. The benefit to the owner, faster completion, lower HVAC costs while increasing usable floor area and occupant thermal comfort.
The benefits of this envelope system were compared to other typical systems by the Glumac Energy team. This paper will study the energy performance of the CCAPP system on building’s energy related carbon emissions. Utilizing energy models from real buildings, the Clark Pacific CCAPP system was compared against various traditional envelope systems (stucco walls with punched windows, window walls and curtain walls) for a typical office building and a high-rise residential tower. Each building was analyzed in various climate zones across the western United States to better understand the regional impact in energy usage and cost. It will also demonstrate that more than 2” of insulation will not have a significant impact on performance.
This paper will showcase both the technical details of the CCAPP envelope system and a comprehensive energy analysis to show the impact that the CCAPP system can have to reduce a building’s energy related carbon emissions.
Authors
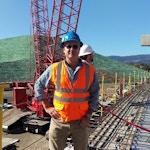
Mike Ryan
Director of Product Development Facades Division
Clark Pacific
mryan@clarkpacific.com
Brian Stern
Regional Energy Director
Glumac
BSTERN@GLUMAC.COM
Michael Adams
Senior Energy Analyst
Glumac
madams@glumac.com
Keywords
Introduction
CCAPP Facade DetailsCCAPP Pre-Glazed Panel View
Utilization of heavy-mass materials in building construction is a practice that impacts construction schedule, budget & material selection. By quantifying the benefits of a project’s
Access Restricted
Method
The DOE-2 based software package eQuest 3.65 has been used to simulate the energy performance of the buildings. Included in the following sections is a description of how this tool
Access Restricted
Data & Results
Commercial Office Results
The comparative office building utilized in this study is a 6-story, 235,000 square foot, boomerang shaped office building with a typical office building floorplan & layout. The HVAC
Access Restricted
Explanation
The envelope system study compared, the CCAPP envelope system with thermally broken windows in four (4) different climate zones. The CCAPP envelope system was compared with two (2) other typical
Access Restricted
Conclusion and Future Work
The CCAPP envelope system was beneficial in most climates and parametric runs. The CCAPP system has the most benefit in heating dominated climates.
In the near future Ultra High Strength Concrete’s
Access Restricted
Rights and Permissions
All images were provided by Glumac and Clark Pacific