Embodied Carbon Of Timber Unitized Curtain Wall
The Impact of Using Timber Instead of Aluminum for Mullions
Presented on October 12, 2022 at Facade Tectonics 2022 World Congress
Sign in and Register
Create an Account
Overview
Abstract
The building envelope is at the intersection of embodied and operational emissions. Curtain wall specifically could play an important role in reducing life cycle impacts of the built environment as a whole because of its prevalence in modern architecture. Unitized systems tend to be more durable than stick-built systems thanks to the tight precision that can be achieved in a factory environment, and they can meet the erection speed of mass timber structures. Timber as an envelope material has potential advantages over aluminum or steel, including the fact that it is a renewable resource, its low thermal conductivity, and its low embodied carbon. The objectives of this study are to evaluate the upfront embodied carbon of using timber mullions instead of aluminum mullions in unitized curtain wall for a project site in New York and in San Francisco. This study finds that for the production and construction stages combined, a timber system can result in an 11-17% reduction in global warming potential depending on the geographic scenario and glass manufacturer location. In addition, different project locations benefit differently from the global supply chain, and choosing a local glass manufacturer matters. Development of a timber unitized curtain wall system is a worthwhile effort as the building industry tries to reduce its environmental impacts.
Authors

Isabelle Hens, LEED AP BD+C, WELL AP, EIT
Environmental Designer
Atelier Ten
isabelle.hens@gmail.com
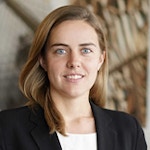
Sophie Pennetier
Associate Director - Special Projects
Enclos
spennetier@enclos.com
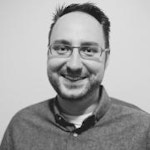
Simon Schleicher
Associate Professor
University of California, Berkeley
simon_s@berkeley.edu
Keywords
1. Introduction
Reducing the embodied carbon of unitized curtain walls can be addressed in several ways, including the choice of materials and their supply chain. Aluminum has a very high thermal conductivity and does therefore require thermal breaks using low-conductivity materials such as PVC, neoprene rubber, polyurethane, and polyester-reinforced nylon (Whole Building Design Guide, 2016), which often have high embodied carbon values. In addition, aluminum itself has a high embodied carbon value as well in comparison to other materials including timber. Aluminum does have a high recyclability potential, but this is often insufficiently leveraged. While timber does not allow for complex extruded profiles, it does have a low thermal conductivity and a low embodied carbon. Thanks to innovations in engineered timber and evolutions in building codes, the number of large-scale timber building projects has increased massively over the past few years. The large scale of these projects demands unitized facade systems, and there is a demand to extend the use of timber to the facade to visually express sustainability. While timber is already being used for stick-built curtain wall systems, its use in unitized systems is limited. This study aims to develop an understanding of the possibilities and implications of applying timber unitized curtain wall on a more widespread scale and evaluate the environmental benefits in comparison to aluminum unitized curtain wall. Given the limited leveraging of aluminum recycling potential in the building industry, the growing volume of new construction relative to recyclable stock, and despite the current non-circular use of timber, upfront carbon emissions and their immediate impact on the environment urge the façade industry to consider timber amongst other low carbon materials.
2. Methods
This study aims to quantify the environmental impacts of a timber unitized curtain wall system in comparison to an aluminum system in terms of global warming potential (GWP) for two
Access Restricted
3. Results
3.1 Production Stages
The production stages cover raw material supply, transport to the factory, and manufacturing. Figure 1 shows the GWP for the aluminum and timber curtain wall systems per
Access Restricted
4. Discussion and Conclusions
To reduce its life-cycle environmental impacts, the building industry needs to reduce consumption of raw materials and energy. The building envelope can contribute significantly to both the embodied and operational
Access Restricted
Acknowledgements
I would like to thank Simon Schleicher and Sophie Pennetier for their continued guidance and input on this research project.
Rights and Permissions
AGC Glass Europe. (2019). Environmental and Health Product Declaration: Safety Double Glazing Units.
American Wood Council & Canadian Wood Council. (2013). Environmental Product Declaration: North American Glued Laminated Timbers.
Hartwell, R., & Overend, M. (2019). Unlocking the Re-use Potential of Glass Façade Systems. GPD Glass Performance Days 2019, 273–280.
North American Insulation Manufacturers Association. (2018). Environmental Product Declaration: Mineral Wool Board.
SeaRates (2021). SeaRates. https://www.searates.com/servi... Aluminum Association. (2014). Environmental Product Declaration: Extruded Aluminum.
Walter P Moore (n.d.). Stewardship Report: Embodied Carbon. Walter P Moore.
Whole Building Design Guide. (2016). Curtain walls. WBDG. https://www.wbdg.org/guides-specifications/building-envelope-design-guide/fenestration-systems/curtain-walls