Digital Enablement for Manufacturing
Automating Digital Workflows for Direct Direct Digital Manufacturing
Presented on October 13, 2022 at Facade Tectonics 2022 World Congress
Sign in and Register
Create an Account
Overview
Abstract
Architectural design freedom achieved on high-end projects currently costs over $1,000/sq. Ft. Building materials have long been relegated to plane stock - flat rectangles. Customization is prohibitively expensive for most projects; and standard methods and materials cannot address the digital divide of what has been possible to design in computers for the last 20 years, yet unattainable to construct. New materials, digital workflows and fabrication technologies offer extraordinary efficiencies and opportunities to change this.
Today we turn a corner to witness and establish a building material system that packages up the collective novelties as affordable and standardized products to freely design with. DDM(Direct Digital Manufacturing) powered by robust DFM(Design for Manufacturing) methodologies can chart a path forward. DDM is the process of fabricating elements directly from a CAD file. There are many forms of DDM, including but not limited to 3D printing, laser cutting, CNC routing, multi-axis robotic processes and other machine tools that run off of digital tool paths. DFM(Design for Manufacturing) involves efficiently designing a complex part, assembly or system relative to material and tooling requirements. Here physical and digital technologies drive more accurate, flexible, responsive, and interconnected products. They also offer a journey out of ‘cookie-cutter’ building designs. When we combine DDM with DFM we can begin to create powerful digitized building systems that can advance design innovation via mass-customization and form driven design while also securing manufacturing accuracies and quality to ensure design intent. This paper will discuss the efficacy of 3D modeling relative to a building product that amalgamates innovative materials, digitzations and advanced fabrication technologies to produce unprecedented 3D building enclosures.
Authors
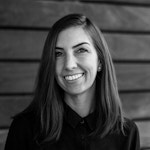
Melody Rees
Director of Design
Branch Technology
melody@branch.technology
Keywords
Introduction and Background
The completion of a first-of-a-kind-project for TVFCU (Tennessee Valley Federal Credit Union) to create fluid, formal and uniquely 3D articulating façade panels represents a roadmap to mass-customized building products and a market demand for such a novel product. The project and product offered a promise to close the digital divide in conceptual architecture of what was once impossible to construct or afford. It touted a potential for outstanding building performance metrics and harnessed new methods of direct digital manufacturing technologies like large-scale 3D printing and the use of robotics. While the project came with much success, the principles and methods were in their infancy with opportunity for improvement.
This paper identifies the lessons learned from the TVFCU project located in Chattanooga, TN and demonstrates those learnings on a second project that followed suit— The Monroe Parking Garage located in Huntsville, AL. This paper will specifically focus on problems and solutions related to the efficacy of 3D modeling for manufacturing. We concentrate on the development of a digital production workflow, chiefly computational operations and procedures imposed by software tools with the goal of automating highly accurate models. We discuss the challenges of applying the workflows on real-world projects with timelines and budgets all the while creating a scalable system capable of bringing fully tested, engineered, repeatable and lasting building products to market quickly and simultaneously.
First, it is important to understand the process flow from design to fabrication and the needs of manufacturing. In the case of the articulated façade panels, the process begins with a single design surface input that is panelized into discrete panels per code compliant testing, manufacturing capabilities and architectural alignments. The panels are created as watertight volumes with which to crunch necessary components into. Templating is used to house standard details and geometric logics for 3D printing volumes, milling surfaces, embedded steel and ample quality control data points. Templates are instantiated across the many panels on a building as a way to produce highly stable, predictable, repeatable parts for manufacturing. This process is complex with many interrelated elements. Sub assemblies for each material process are then pulled into a path planning process where KRL(Kuka Robot Language) or other machine source files are produced. Path planning is the process of solving kinematically possible, collision-free paths for the robot to traverse in 3D space with a given mechanical tool. These tasks are a function of the overall shop ticket that is submitted to the shop floor for the production of any project panel. We call this geometrical component crunching ‘Part Generation’.
Identifying Challenges
The TVFCU project used Rhinoceros (McNeel, Version 6) and Grasshopper 3D (Rutten and McNeel, 2018) to complete the Part Generation process. Limitations were discovered on two fronts. The first issue
Access Restricted
Process
The team sought to resolve the process shortcomings by changing software platforms. Multiple platforms were evaluated in search of one robust and scalable platform that enabled DFM(Design for Manufacturing). The
Access Restricted
Conclusion and Future Work
Evolving a robust digital production process was critical to the development of the mass-customized articulated façade panel product as executed on the Monroe Parking Garage project and its predecessor, TVFCU
Access Restricted
Acknowledgements
Tennessee Valley Federal Credit Union Flagship Branch in Chattanooga, TN.
Client: Tennessee Valley Federal Credit Union
Architect: River Street Architecture
Panel Design/Fabrication: Branch Technology
Rain Screen Carrier System: SFS - Nvelope
General Contractor: Construction Consultants, Inc.
Monroe Parking Garage in Huntsville, AL
Client: City of Huntsville
Architect: Fuqua Partners and Architects
Panel Design/Fabrication: Branch Technology
Structural Engineer: Larson Engineering
General Contractor: Turner Construction
Rights and Permissions
McKinsey & Company. 2020. The next normal in construction. How disruption is reshaping the world’s largest ecosystem. Maria João Ribeirinho, Jan Mischke, Gernot Strube, Erik Sjödin, Jose Luis Blanco, Rob Palter, Jonas.
Dassault Systèmes. April 17th 2019. Realizing Creative Inspirations Through Digital Continuity: CO Architects Leverages Generative Design Tools for Continuous Architectural Design & Engineering Innovations, https://coarchitects.com/realizing-creative-inspirations-through-digital-continuity/
Müge Tetika, Antti Peltokorpia, Olli Seppänena, Jan Holmströmb. Automation in Construction. December 2021. Direct digital construction: Technology-based operations management practice for continuous improvement of construction industry performance. 1-13. journal homepage: www.elsevier.com/locate/autcon
Daniel Davis. August 27th 2020. Architects Versus Autodesk. Architect Magazine. The Journal of the American Institute of Architects. https://www.architectmagazine.com/technology/architects-versus-autodesk_o
David Celanto. 2007 Innovate or Perish: New Technologies and Architecture’s Future. www.harvarddesignmagazine.org/issues/26/innovate-or-perish-new-technologies-and-architectures-future . Harvard Design Magazine. New Skyscrapers in Megacities on a Warming Globe. Volume 26.
Ian Gibson, David W. Rosen, Brent Stucker. 2010. Additive Manufacturing Technologies. Rapid Prototyping to Direct Digital Manufacturing, https://link.springer.com/book/10.1007/978-1-4419-1120-9