Detailing & Engineering Of Complex Geometry Copper Panels
A case study in developing a custom-designed copper panel rain screen system
Presented on October 10, 2024 at Facade Tectonics 2024 World Congress
Sign in and Register
Create an Account
Overview
Abstract
Paper Abstract with photos and illustrations
Detailing and Engineering of copper panels with complex geometries:
A case study in developing a custom-designed copper panel rain-screen system for an award-winning and widely published façade project:
Ledger City Center – Bentonville, Arkansas
Summary of the paper description:
The project in this case study is a 6-story bikeable office building in Bentonville, Arkansas. It is designed by Michel Rojkind, Callaghan Horiuchi, and Marlon Blackwell Architects. It opened in Spring 2023.
The project envelope consists of alternating ribbons of glazing and copper panels that follow floor slabs and ramps up and down the building. The copper panels, the focus of this paper, clad an area of 50,000 sq ft with over 5,300 individual panels, consisting of 600 uniquely-shaped panel types.
The copper panels were unusually wide, so joints align with the curtain wall 5 ft module. These panels had a 3D shape that required developing a custom flat seam interlock system and attachment. The design of the façade resulted in many unique parts that needed to be tracked through fabrication and installation.
What was done:
The paper will explore how the geometry of the panels was resolved to allow fabrication and installation. And how the system was engineered to resolve the unusually wide copper panels and minimize oil canning.
How it was done:
Multiple tabletop mock-ups were developed to study the different panel types and their assembly. This physical testing led to the development of unique shapes that can interlock together while staying true to the design intent.
Engineering of a custom clip system was required to attach the panels to the building structure.
In terms of digital fabrication, despite the high number of unique parts to accommodate myriad panel typologies, one single Revit family was developed to generate 98% of the total panels used on the project. The Revit family also provided all the information and panel detailing needed for fabrication, quantities, sequencing, etc.
Results
A single panel had to be split into multiple components to enable fabrication and reassembly without compromising the overall geometry of the façade and the project's design intent.
Despite the high number of unique panels and a large number of parts, the panel system was fabricated and installed with no need for field measurements and almost no field modification.
Who would be interested
Architects, General Contractors, Installers, fabricators, Parametric design experts
Authors
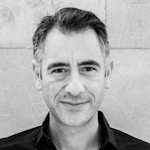
Becher Eli Neme
Founding Principal
Neme Design Studio
becher@nemeds.com
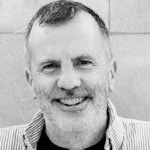
Thomas Johnson
Associate Principal
Neme Design Studio
tom@nemeds.com
Keywords
Paper content
This paper will review the key steps for the successful use of copper in both a wide format, a complex geometry, and being built to hold to dimensions while the
Access Restricted
Acknowledgements
Special thanks to Ethan Kaplan, Marlon Blackwell Architects, James Russel, Harness roofing, Greg Kimm, Dissimilar metal design, Mahmoud Zadeh, RJC engineers, and Nicholette Ward, Neme Design Studio, for their contribution to this paper.
We also recognize the contributions of Marco Broccardo for the insight on detailing and engineering of the panels' attachment system and Elan Lipson for the development of the revit model and families. Their efforts were crucial to the success of this project.
Project Team involved with exterior enclosure scope:
Design Architects: Marlon Blackwell Architects, Michel Rojkind, and Callaghan Horiuchi Architects
Design Team façade consultant: Studio NYL
General Contractor: Nabohlz Construction
Installation Team: Harness Roofing / JAMA engineers
Fabrication Team: Dissimilar Metal Design / Neme Design Studio, RJC engineers